一、智能排产能否破解传统生产计划的“拍脑袋”困局?
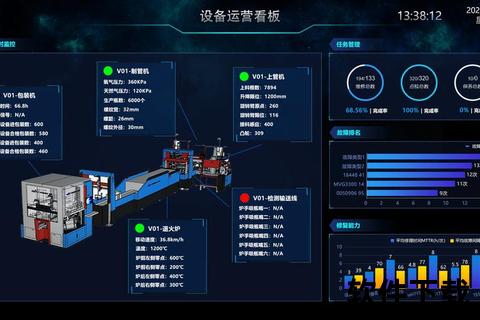
传统制造业长期面临一个矛盾:市场需求日益个性化,但生产计划却依赖人工经验。某汽车零部件企业曾因计划失误导致2000万元库存积压,而另一家电子代工厂因排产混乱造成30%订单延期交付。这些案例暴露出传统排产模式在效率与精确性上的致命短板。
智能排产软件通过算法模型实现了颠覆性变革。以共进电子为例,这家年产值超百亿的ODM企业引入APS系统后,日计划排产时间从4-6小时缩短至0.5小时,订单交付及时率提升20%。系统通过整合ERP、MES数据,实时计算设备产能、物料库存、工艺约束等200余项参数,将原本需要人工协调的复杂排产转化为秒级运算。更关键的是,系统能动态响应突发状况——当某型号芯片突发短缺时,算法自动触发替代料方案并调整10条产线的生产顺序,避免停工损失。
这种革新不仅体现在效率层面。某锂电池制造企业的实践显示,智能排产使设备利用率从68%提升至85%,同时将模具切换时间压缩40%。这验证了算法驱动下的资源优化配置能力,传统模式下难以兼顾的效率与成本问题,在智能系统里找到了平衡点。
二、资源优化配置如何突破"人机料法环"的协同壁垒?
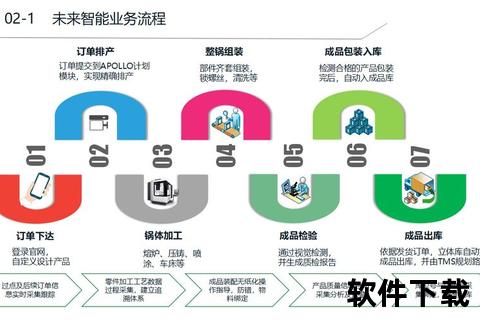
制造业资源协调如同交响乐演奏,任何声部的失调都会破坏整体效果。某家电企业曾因注塑与总装车间产能不匹配,每月产生300小时设备闲置。智能排产软件的价值,在于将离散的资源要素转化为可计算的优化模型。
万界星空科技的MES系统在印刷行业创造了典型案例。通过部署智能排产模块,某包装企业实现:
设备状态感知准确率达99.8%
物料齐套分析效率提升15倍
异常响应时间缩短至5分钟内
这得益于系统构建的三层优化体系:底层物联网实时采集2000余个设备参数,中层算法动态调度生产任务,顶层可视化看板实现跨部门协同。当某批次原料检测不合格时,系统在30秒内重新规划5条产线的生产序列,并同步更新供应商补货计划。
更值得关注的是人力资源的精准配置。某汽车主机厂运用智能排产后,通过技能矩阵与任务需求匹配,将高技能人员利用率从65%提升至92%,同时减少25%的临时用工成本。这种"数字孪生"式的人力调度,正在重塑制造业的人力资源管理模式。
三、生产流程革新如何驱动产业链协同创新?
单个企业的效率提升已不足以应对全球化竞争,智能排产的价值正在向产业链延伸。某消费电子品牌商联合12家核心供应商构建协同计划平台后,整体库存周转率提升40%,新品上市周期缩短25天。这揭示出智能排产系统的深层价值——成为供应链协同的"数字纽带"。
工业4.0时代的典型案例发生在某航空制造集团。其智能排产系统整合了:
2000余家供应商的交付数据
15个生产基地的产能信息
30万种零部件的替代方案
当某型号发动机延迟交付时,系统自动启动应急方案:调整3个国家7家工厂的生产计划,重新分配200台数控机床任务,并触发海运转空运的物流方案。这种全局优化能力,使该企业客户满意度提升18个百分点。
更深远的影响体现在商业模式的创新。某服装企业通过智能排产系统支撑C2M模式,将定制订单交付周期从21天压缩至72小时。系统实时对接2000家门店销售数据,动态调整50条柔性产线的生产节奏,实现"销售即排产"的敏捷制造。
面对智能排产带来的变革机遇,企业应采取三步走策略:
1. 基础诊断:评估现有信息化成熟度,优先补全设备联网、数据标准化等基础建设
2. 场景突破:选择订单波动大、工艺复杂的业务单元先行试点,如某企业从SMT车间突破,3个月实现排产效率提升300%
3. 生态构建:通过API接口打通上下游系统,某机械制造商连接供应商系统后,物料齐套率从78%提升至95%
智能排产软件的高效驱动,正在重构制造业的价值创造逻辑。当算法开始指挥生产交响乐,资源优化配置不再停留在理论层面,而是转化为实实在在的竞争优势。这场由数字技术引发的生产流程革新,终将重塑整个制造业的生态格局。
相关文章:
文章已关闭评论!