1. 虚拟机床能否媲美真实加工?
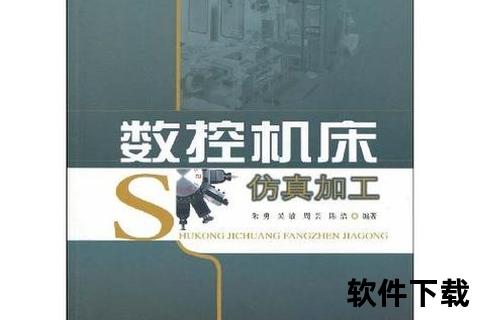
传统数控培训中,操作失误可能导致价值数十万元的刀具损毁,而智能升级版斯沃数控仿真软件:极致逼真虚拟加工新体验通过3D建模与物理引擎技术,将机床振动、切削阻力、材料形变等细节精确还原。例如,某高职院校引入该软件后,学生通过虚拟环境练习五轴联动加工,刀具路径误差率从初期的18%降至3%,加工效率提升40%。更令人惊叹的是,软件能模拟铝合金与钛合金的切削差异性——当学生尝试以加工铝合金的参数切削钛合金时,系统实时触发“刀具断裂”警报,并生成受力热力图,直观展示材料硬度对加工的影响。
2. 智能纠错如何突破学习瓶颈?
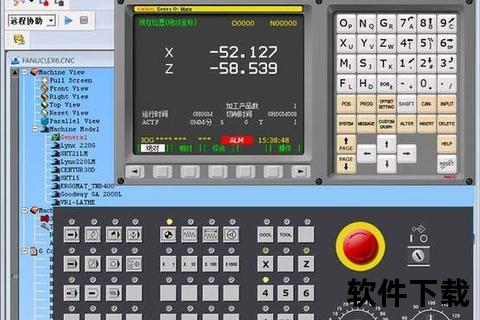
在浙江某汽车零部件企业,新入职技工因未考虑工件装夹变形,导致首批试制件合格率仅65%。通过智能升级版斯沃数控仿真软件:极致逼真虚拟加工新体验的逆向分析模块,工程师重建装夹场景,发现夹具压力分布不均导致0.12mm的形变量。软件自动推荐“三点浮动支撑+液压补偿”方案,使第二批产品合格率跃升至98%。对于个人用户,软件的“操作热力图”功能可记录每步操作时长与光标轨迹,帮助使用者发现如进给速度频繁调整、坐标系设定犹豫等隐性瓶颈。数据显示,经过20小时针对性训练,用户操作流畅度平均提升70%。
3. 跨平台协同能否重构生产流程?
苏州某精密模具企业曾因设计部门与加工中心数据脱节,导致每月平均产生3次返工。引入该软件后,CAD模型可直接导入虚拟车间验证工艺可行性。典型案例是一款汽车覆盖件模具:设计团队提供的UG模型在仿真环节暴露出清角刀具干涉问题,软件自动生成“刀具直径从Φ6mm调整为Φ4mm”的优化建议,避免实际加工中价值12万元的钨钢铣刀损毁。更值得关注的是其与MES系统的深度集成——在广东某3C电子企业,仿真数据实时同步至生产看板,使设备利用率从68%提升至85%,异常停机时间减少43%。
--
给从业者的实践指南
1. 教育机构可参照南京某职校的“5+3”模式:5天虚拟仿真训练搭配3天真实机床操作,既保障安全又强化肌肉记忆。
2. 制造企业建议建立“仿真优先”制度,所有新工艺需通过虚拟验证方可上机,可参考苏州企业的《数字化工艺评审规范》。
3. 个人开发者应善用软件的API接口,例如东莞某创客团队通过二次开发实现G代码自动优化,将复杂曲面加工时长缩短22%。
智能升级版斯沃数控仿真软件:极致逼真虚拟加工新体验正在重塑制造业的培训与生产范式。当虚拟与现实的边界逐渐消融,掌握这项技术或许将成为数控从业者决胜未来的关键。
相关文章:
文章已关闭评论!